技術提案
CASE1:「磨き+コーティング」でトータルコストの低減
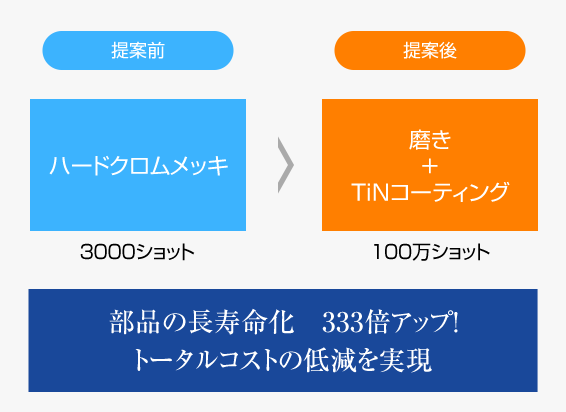
課題・問題点
金型の耐久性や機能性を向上させコストを下げたい。その為に金型部品において何か良い改良方法はありますか。
提案内容
現状ハードクロムメッキを施していた金型部品を、磨き工程と摩耗性や耐蝕性に優れるTINコーティングへ工法の変更を提案。
その結果、部品寿命が3000ショット→100万ショットへ333倍アップ!コーティング被膜を見据えて加工精度を調整するなど、独自の技術力とノウハウで、性能の向上と共にトータルコストの低減を実現しました。
CASE2:切削~焼き入れ~研磨(仕上げ)の「一貫対応」で、納期短縮と品質の安定を実現
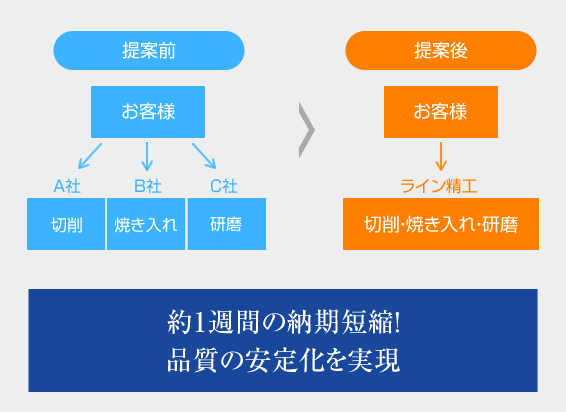
課題・問題点
現在「切削」「焼き入れ」「研磨(仕上げ)」をそれぞれ別の協力メーカーに依頼しています。
しかし、多くの管理工数がかかり、品質にもバラつきが生じてしまうため、改善できないでしょうか?
提案内容
ライン精工では、切削加工~焼き入れ~研磨(仕上げ)まで一貫して対応可能です。
生産を一元化することにより、お客様の管理工数を削減すると共に、約1週間の納期短縮も実現しました。
また品質面においても、弊社にて一貫して品質保証を行うので、品質の安定化を実現。お客様にご安心頂ける製品の供給が可能となりました。
CASE3:加工方法の転換による、部品精度の向上とリードタイムの短縮
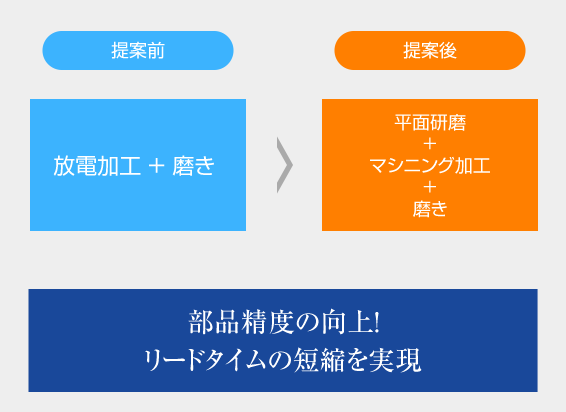
課題・問題点
現在の加工方法だと、凹凸形状が崩れてしまうことがあり困っています。
形状を崩さず加工する方法はありますか。
提案内容
工法転換を提案しました。従来の型彫り放電加工→磨き(仕上げ)という工程から、研削加工(凹凸形状出し)→切削加工(高速マシニングセンター)→磨き(仕上げ)へ変更。
磨き工程においても、ダイヤモンドを練りこんだゴムのショットブラストに変更することにより、形状を崩さず安定して製作することができました。
その結果、部品精度の向上と安定した形状出しを実現しました。
また、マシニングセンターを夜間運転することにより、リードタイムの短縮も可能となりました。
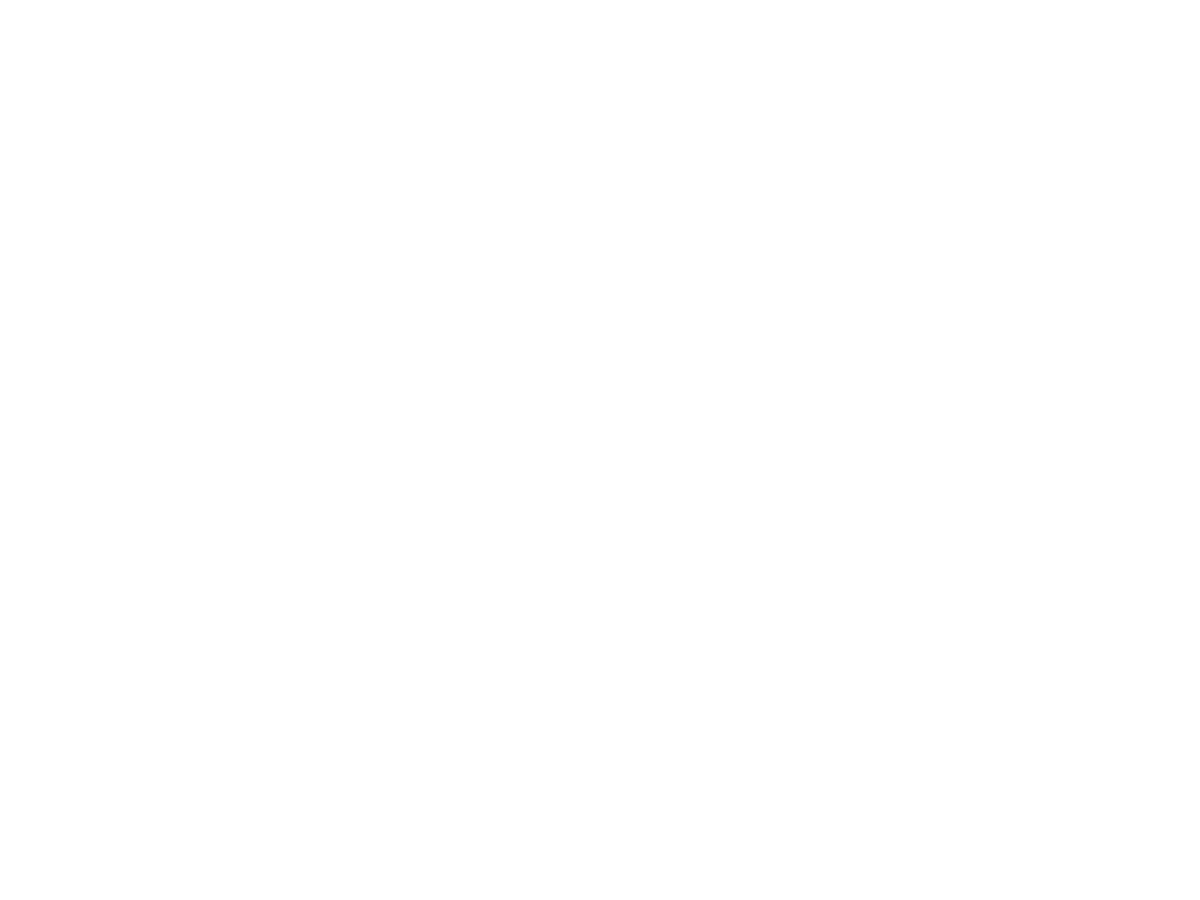
ミクロン単位での精度が必要な金型部品の製作はもちろん、医療・航空機・自動車分野で必要とされる精密部品等、材料手配から納入まで一貫して対応が可能です。
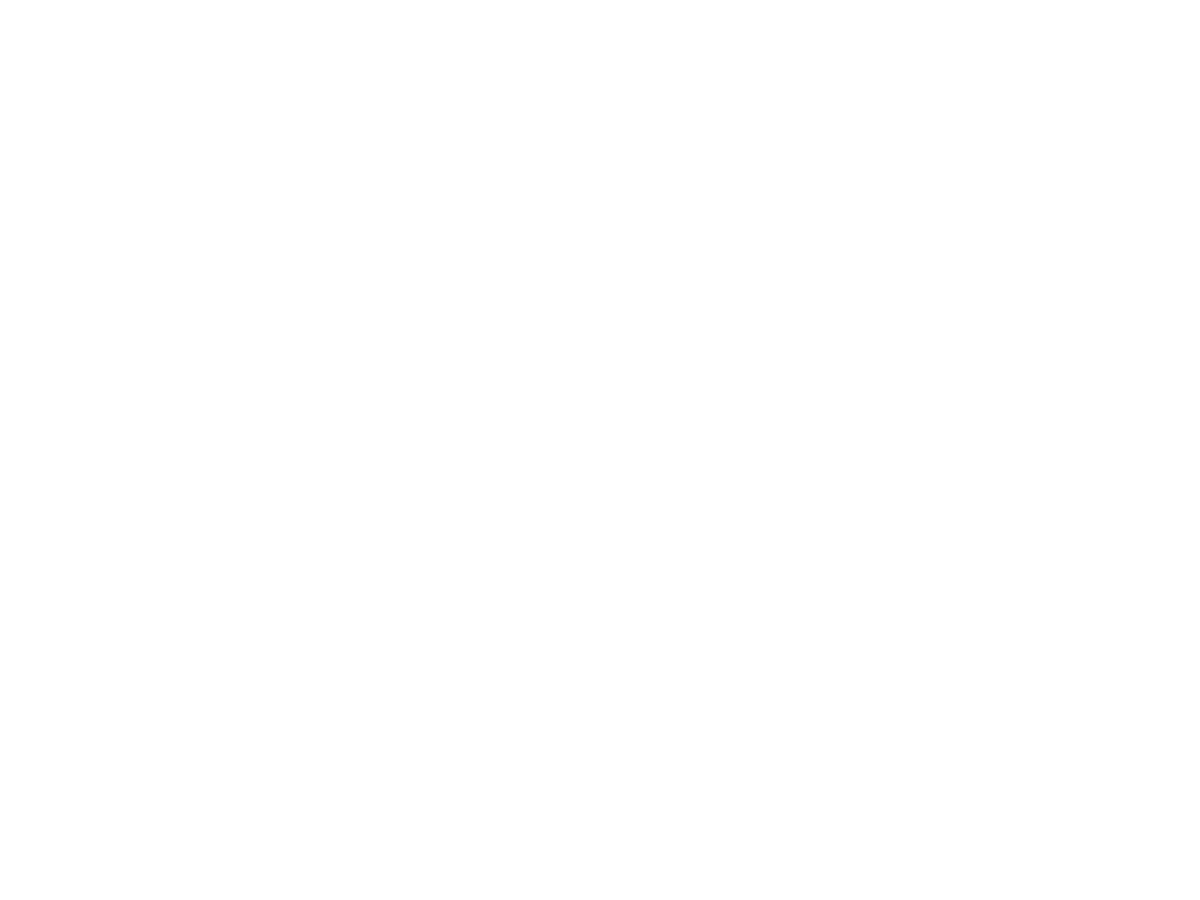
冷間鍛造型や樹脂金型、粉末成型金型、プレス・深絞り型部品の中でも、特に硬度が高く、面粗さや1ミクロン単位の加工精度を必要とする、金型部品加工を行っています。
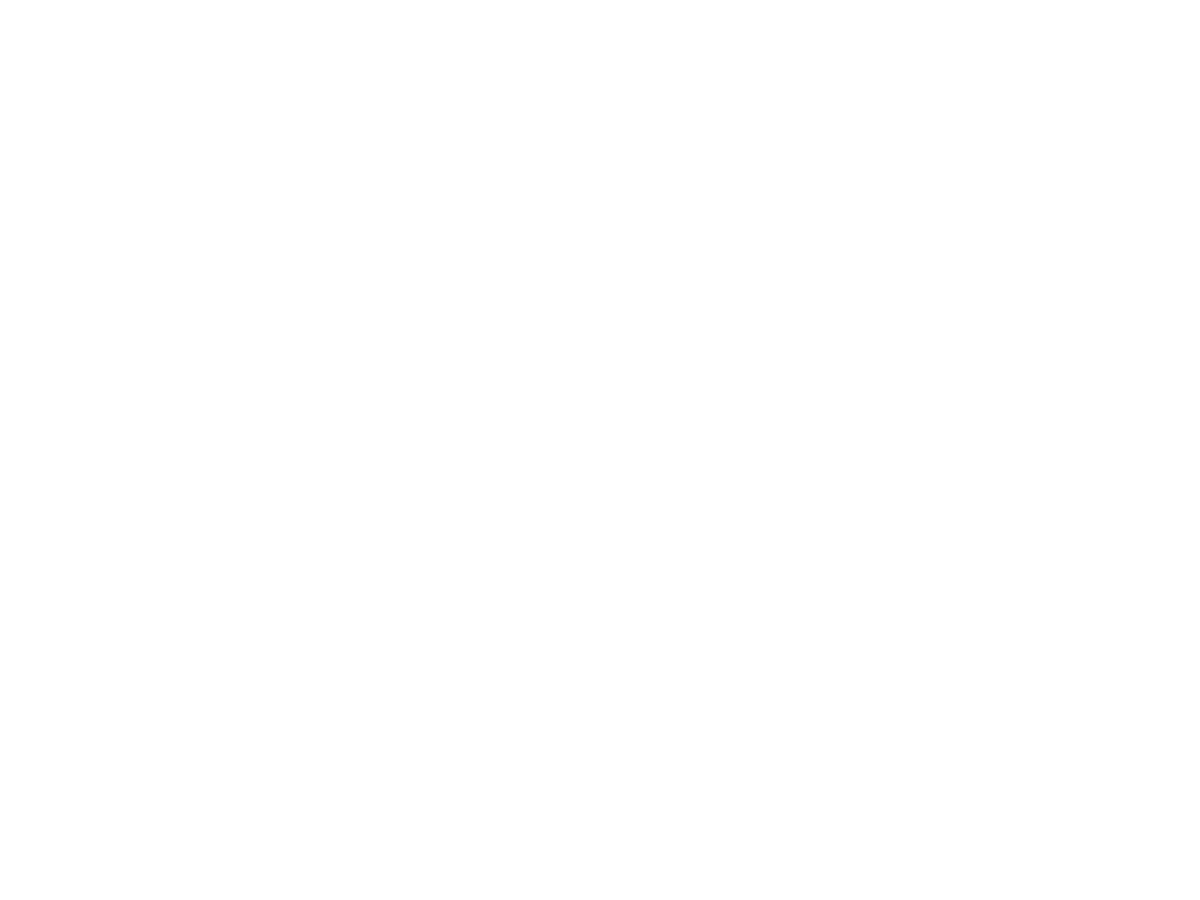
医療・航空機・自動車分野で必要とされる精密部品や、ミクロンレベルの治工具・ゲージ等、材料手配から完成品の納入まで、一貫生産でお届けします。